Overview of all the company Workshop
Metal Processing
The Workshop Total Area is About 8880 m2 Serviced by (Qty 8 ) 10 Tons Overhead Cranes
The workshop is equipped with modern and Automated Metal Plate Cutting Machines including CNC Plasma Cutting Machines able to cut upto 40 mm Steel and Aluminum plate thickness ,Automatic Gas Cutting Machine to cut upto 80 mm Steel and Aluminum plate thickness, Mechanical Cutting Machines , Hydraulic Presses upto 800 Ton and Rollers to be able to deal with up to 35 mm thickness of 8 meter plate width capitalizing all the essential process ( Marking – Cutting- Forming ) in all types of shipbuilding metals (Steel – Stainless Steel –Aluminum ) , attached to the workshop a 6000 m2 stockyard for the Plates and Sections,
Unit Assembly & Welding
The Workshop Total Area is About 8880 m2 Serviced by (Qty 8 ) 10 Tons Overhead Cranes
READ LESS
In line with the Metal Processing Shop comes immediately the unit assembly and Welding Workshop. Four spacious bays each specialized in certain product type forming the whole area occupied by the subject shop.
The first Bay is specialized in the assembly & welding of the flat section (plating together with longitudinal & transverse stiffening mesh and brackets thereto) of total weight not to exceed 16 tons which is the maximum lifting capacity of the overhead cranes available in the workshop.
Bay Number 2 comes next where the assembly & Automatic submerged arc welding stand is located at the entrance of the bay for the purpose of providing huge welded flat panels to various bays of the workshop and generally for the shipyard various needs including the bulkheads and the small decks to be Assembled and Welded in the subject bay.
Bay number 3 comes next where small Sections /Units of stiffened floors and girders, built up web frames, deck beams are assembled and welded using mainly Semi-Automatic CO2 Flux cored wires.
Bay Number 4 comes next where the slightly curved and framed Sections /Units are assembled and welded in the same way as that of bay 3 It is normally that all the units/sections to be inspected by the QC staff attending permanently the workshop and any NDT to be applied to all built sections prior to transported to the block workshop.
Block Assembly and Welding
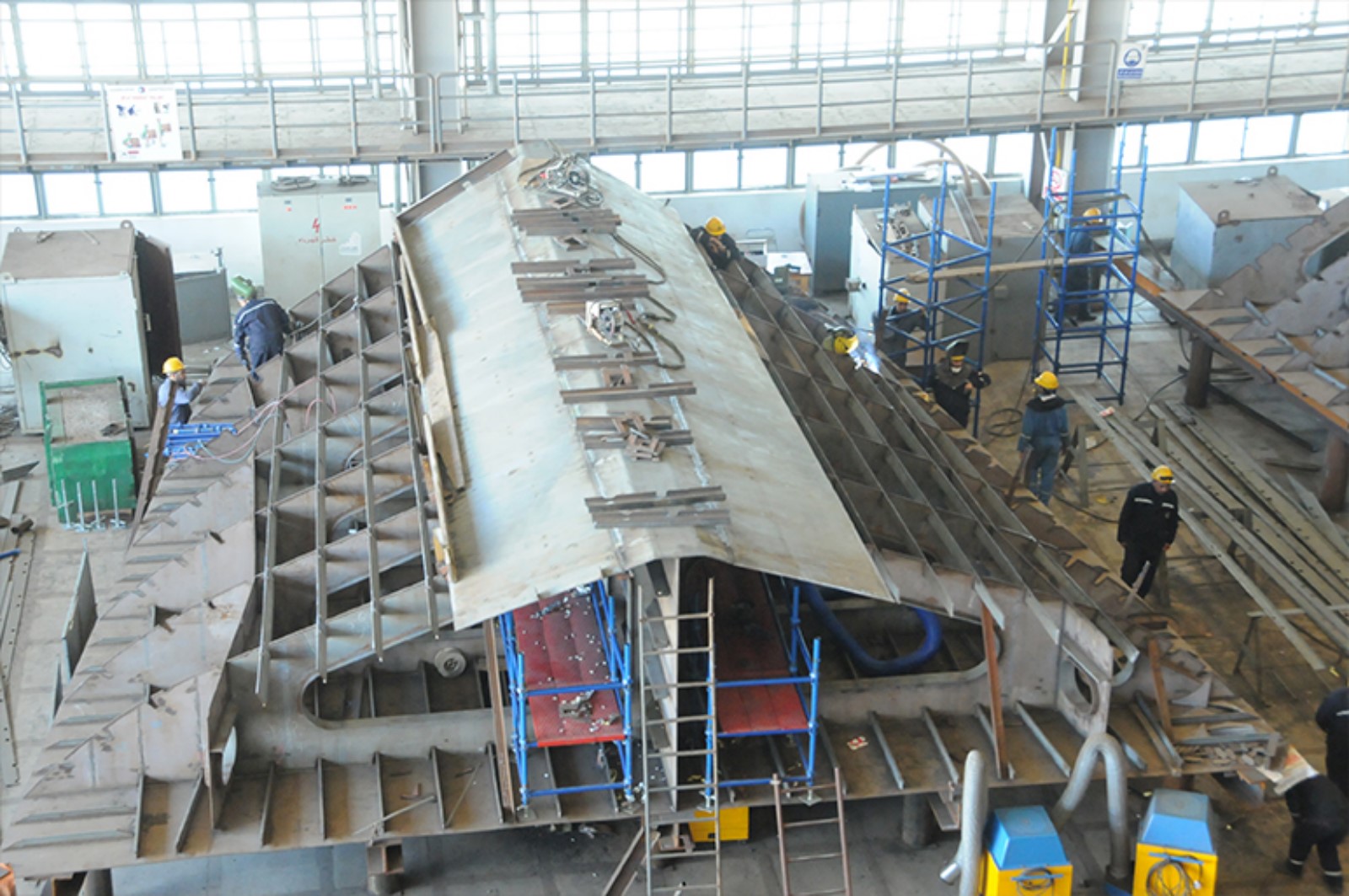
The Workshop Total Area is about 18711 m2 Equipped with 8 Cranes 50 Tons Each and Another 8 of 16 Tons Each Overhead Cranes.
READ MORE
Volumetric Blocks up to 120 tons are assembled out of the sub sections and sections supplied by unit assembly and welding workshop using the various types of mechanized and /or manual process of welding as appropriate on flat stand and/or template stands depends on whether the specified block of fairly straight lines or having 3D curved and figured outlines, QC shall took place for approval then transported using flatbed trailer to blasting and painting workshop and then to flat area and/or building berth.
All Non-Destructive testing as specified are to be carried out i
Blasting, Painting and Coating
The Shop is one of the added value process to the shipyard established during the upgrade process, about 4446 m² area, is essentially provide the shoting and/or grit blasting and coating for various blocks and sections prior to final transfer and mounting on the building berth.
The shop consists of three compartments one for the blasting process and two for coating. The coating shop is mainly provided with various systems, Steel Shot and/or Grit Recovery, Vacuum Recovery, Partial Dust Removing, Full Ventilation and Dust Removing, Dehumidification and Air Supply, Paint Spraying, Compressed Air, Environment-Friendly exhaust and environment-friendly air supply.
In addition to the foregoing the workshop is also carrying out ship insulation works, thermal, fire and sound insulation onboard various ship Deck covering works of various ships types is also one of the principal activities of the workshop
Inclined Berth Assembly, Mounting, Junction & Welding
The vessels are launched using the launching cradles which to be prepared to suit the various hulls of different ship frame and then after to be slid down on the inclined sliding ways.

The various blocks and accumulated huge blocks that accomplished in the block shop and those at the pre-berth area are transported to either the northern or the Southern Berths for further assembly, mounting and erection welding, machinery installation, shaft alignment, controls, mooring equipment are all carried out to the satisfaction of attending surveyors and in accordance with the relevant class requirements, all controlled by the adequately qualified quality control personnel, whom as essential part of their job supervise, assess the various testing requirements NDT, leak tests and dimensional check where necessary.
Pipe Fabrication Installation
All piping systems of various ship types including ballast system, cooling system, air ventilation system, air pipes, fuel oil, lube oil & fresh water system, firefighting, salt water and domestic water system are to be manufactured and installed by the Pipe workshop Workforce.
Whether ferrous or non ferrous material (various steel grades, copper, copper alloys, brass, stainless steel of various grades) all are normally cut to size & dimensions &bent to the required ships, welded to flashed, provided with branch pipes
Normally the pipe shop to be equipped with the machines & tools to facilitate the various needs to fabricate the various spools
the hydraulic bending machines vary in pipes diameter to be bent from 10 to 168 mm . with fabrication ability up to 1020 mm pipe diameter with welders certification in accordance with B.V Classification society
. the needed pipes chemical treatment include degreasing , pickling and passivation chemical treatment sinks to treat tubes before and after operation serving
.pipes metal bent vary from cu-ni. , steel , titanium and aluminum .
Leak tests &hydro tests are normally carried out in the workshop prior to transfer onboard the ship for further installation in accordance with schematic& isometric diagrams
The workshop equipped with huge sections for chemical cleaning, preservation of various piping before it is moved out for installation onboard
Passivation of the copper alloys pipes are also applied in the chemical treatment section of the shop
Highly qualified welders of various skill are provided to fulfill the numerous types of welding no-matter the material& alloy type & grade
Machinery Installation
Mechanical workshop main activity is ship's machinery installation in both during ship repairs and ship building activity , in the ship building activities ,the installation stages progressed along the ship building activity with various ships starting from fabrication & installation of various Machinery Seating, Pumps, Compressors, Auxiliary Engines, Main Engines, Shaft line with various bearing thereto all together with the installation of various hydraulic system including (Steering System ,Lifting Appliances, RoRo equipment (lifts, Ramps, Movable Decks, Watertight Door) different classification society dictate specific requirement for some equipment installation including Shaft alignment, main and auxiliary engine leveling, adjustment are considered principal activities due to which the workshop is equipped with the necessary up-to-date tools to fulfill the stated functions(torques spanner, optical sighting tools-tachymeter, laser tracker&digital caliper gauge)
The workshop is also responsible for the installation of air condition system& refrigeration units and other anti-pollution system.
The workshop major activity in addition to the previous ones is to have the lead & supervision of all commissioning of the various systems whether alongside as quay trails or during sea trails
Machining Process
The Machining Workshop is one of the very distinct workshop with special huge and heavy work piece processed items to be processed that fits for the normal ships equipment and element dimension a horizontal lath able to deal with propeller shaft machining and other long pieces with a dimension up to 16 m long , 1 m diameter or other horizontal lath fits for work piece of 10 m long and 2 m diameter.
Huge boring machines that fits for work piece of 4 m x2 m x4 m.
A vertical lath of 2 m x 2 m also serve hugh work piece rarely found in any place but huge ships.
Ships element like Propeller shaft, rudder stocks, stern tube bearings, A’ bracket bearing, rudder cone & propeller hub all with many other wide Varity of miscellaneous ship’s and mechanical parts are all either dressed smooth or undergo turning, milling, boring and/or drilling operations by the virtue of the available machines of various sizes and types either stationary inside the workshop or portable units to carry out several operations on the spot like boring of the stern tube and ‘A’ brackets bearings.
Rudder cones& stock necessary machining, skimming of built up rudder stocks all are done on the special lathes available in the workshop.
Vertical boring of huge castings all being carried out in the subject workshop.
Outfitting
The Workshop is capable of installing Ship’s various accessories that requires highly skilled workers and special installation equipment , accessories like ladders & Accommodation stair ways, windows, doors, deadlight& Skylight are all either fabricated and/or procured and all to be installed, Welded and tested on board by the virtue of well-equipped outfitting workshop which normally provided with highly skilled labor force.
Various air ducts in the accommodation space, Provision stores , Galley equipment, Deck machinery, Access hatches, Hatch covers, Windlass machinery, Capstan, Mooring Equipment, Bollard Bits, Fairleads, Masts etc. are all being manufactured and/or installed on board the ship by highly skilled labour of outfitting w/s
Fiberglass
The Workshop Total Area is about 18711 m2 Equipped with 8 Cranes 50 Tons Each and Another 8 of 16 Tons Each Overhead Cranes.
READ LESS
Volumetric Blocks up to 120 tons are assembled out of the sub sections and sections supplied by unit assembly and welding workshop using the various types of mechanized and /or manual process of welding as appropriate on flat stand and/or template stands depends on whether the specified block of fairly straight lines or having 3D curved and figured outlines, QC shall took place for approval then transported using flatbed trailer to blasting and painting workshop and then to flat area and/or building berth.
All Non-Destructive testing as specified are to be carried out in the Workshops , Welding Defects shall be repaired and retested before finally accepted and released for further activities Air leak tests shall be carried out as specified, to ensure proven air or water tight compartments or tanks